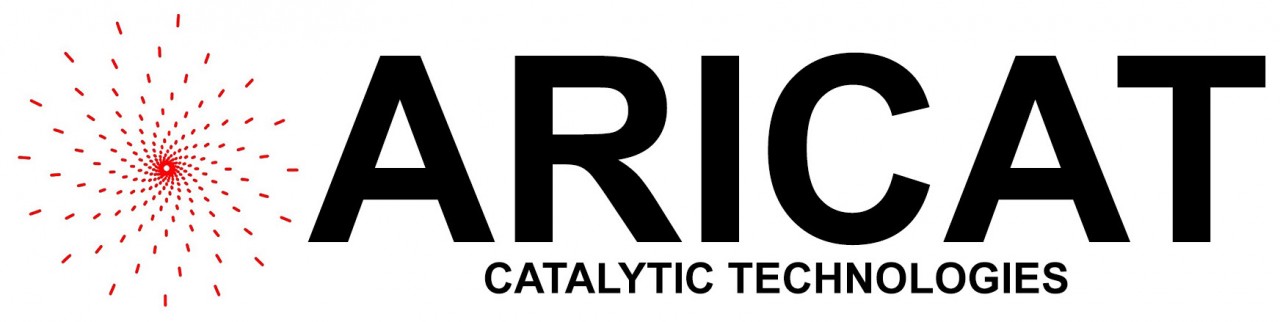
+39 030 9910452 |
info@aricat.it
Ventilated Booster Panel
Campi di applicazione
Gelling of powder coatings on metals
Gelatinisation of powder paints on MDF and HDF
Drying of solvent based paints, water and oil
Heat treatment of paints on plastic material
Powder Coating Powder (Full Treatment-Cure)
Polymerisation of powder coating
Termoforming
Screen printing industry
Textile industry (eg silk-screen printing, thermosetting, non-woven fabrics)
Tanning industry
Ink drying
Preheating before painting
Preheating of materials at the entrance of conventional convection ovens
Latex Gelation after Coating
Thermal treatment of synthetic fibers
Drying of glass (eg decoration, mirrors)
Drying of cars
Drying insulating paints on electrical cables
Drying of products prior to surface treatments (eg sandblasting)
Ink drying on paper
Thermal stabilization of organic products
Vulcanization
Shrinking treatments
Food sector (eg cooking vegetable dehydration)
Ventilation applications
Oil & gas applications (eg heating tubes, instrumentation and workstations in the petrochemical sector)